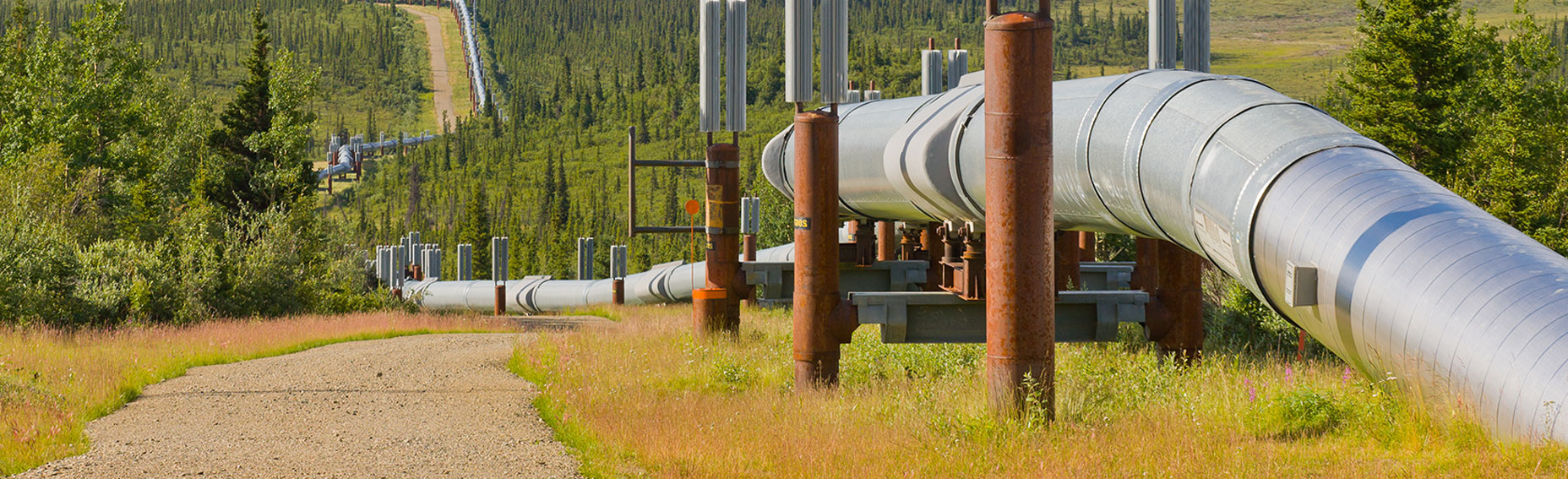
Pipeline Integrity
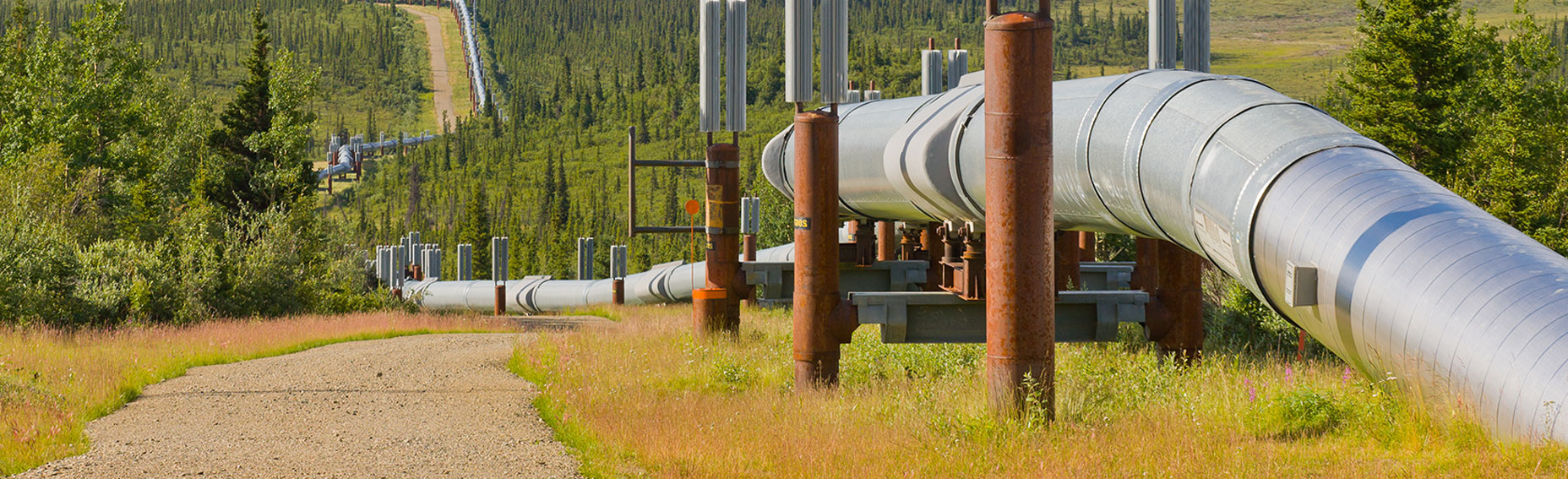
Report a Natural Gas Leak
If you suspect a natural gas leak, evacuate the area immediately and call us from a safe location: 1-800-427-2200
Call 911 promptly, from a safe location, if there is damage resulting in a natural gas leak that may endanger life, cause bodily harm, cause property damage, and/or if you are unable to contact SoCalGas for any reason.
As the nation's largest natural gas distribution utility, we're committed to providing clean, safe and reliable natural gas to our customers. To get natural gas safely from California producers to you, we put significant resources towards improving the safety and integrity of our more than 101,000 miles of natural gas pipelines.
What We Do to Protect You
We're responsible for the inspection of all of our natural gas pipelines. In order to help protect our employees and customers, we take the following safety measures.
Distinctive Natural Gas Odor
We add a distinctive odor to natural gas so leaks can be easily detected. The odor level is monitored at least monthly at different locations to make sure it's adequate. While that odorant makes natural gas easy to recognize, you may not be able to smell leaking gas if:
- You have a diminished sense of smell
- You’re experiencing odor fatigue (normal, temporary inability to distinguish an odor after prolonged exposure to it)
- You have a physical condition such as a common cold, sinus condition or allergies
- You use tobacco, alcohol, drugs and certain medications
- The odor is masked or hidden by other odors that are present
- Pipe and soil conditions have caused odor fade. Odor fade can be caused by adsorption, absorption, oxidation or any combination thereof
Leak Surveys
We conduct leak surveys of our pipelines, typically using combustible natural gas detection equipment. We then prioritize the highest potential risks and make sure they're continuously monitored and repaired promptly.
Pipeline Patrols
Pipeline patrols are performed by trained and qualified individuals within structured scheduled times that meet or exceed Federal and State requirements, depending on various attributes of a facility, to look for indications of any abnormal conditions such as, missing pipeline markers, construction activity, potential gas leaks and other factors that can affect safety and operation of the pipeline.
Exterior Corrosion Control
In order to protect pipelines from external corrosion, we use pipeline coating and cathodic protection. Pipeline coatings prevent corrosive environments from coming into contact with the surface of the pipeline. Cathodic protection systems protect the steel against any voids in the coating by using direct electrical current to counteract the normal external corrosion of a metal pipeline.
Cathodically protected pipe is monitored on an annual basis to verify that the cathodic protection system is functioning properly. Buried steel pipelines installed prior to July 31, 1971 that aren't cathodically protected are surveyed for leaks at a greater frequency. Piping exposed to the atmosphere is inspected for corrosion at least once every three years.
Internal Corrosion Control
We also manage the quality of the natural gas in our system and the system's operation to prevent internal corrosion by monitoring on an annual basis.
Valve Inspection
Valves critical to the isolation of a pipeline segment are inspected once each year and serviced for valve casing leak detection, proper valve identification, adequate lubrication and valve operation.
Underground Vaults
Once a year, we perform routine maintenance and inspection on all underground vaults within our service area, which typically contain pressure-regulating or pressure-limiting equipment. Maintenance and inspection include proper operation of ventilation equipment, structural conditions, and correction of water presence, trash or other foreign substances.
Pipeline Crossings
Sometimes we have to design our natural gas piping system to cross over obstacles - typically freeways, highways, rivers and drainage channels - rather than go underneath them. Regardless of the crossing type, routine inspection and maintenance of all crossings are performed at least once every three years.
Pressure-Relief Devices
Pressure-relief devices at pressure-limiting stations and pressure-regulating stations must have enough capacity to protect the facilities that they're connected to. Each pressure-limiting station, relief device (except rupture discs), signaling device, and pressure-regulating station and its equipment are inspected once per year.
High-Consequence Areas
As part of the Transmission Integrity Management Program instituted in December 2004, a full assessment was completed in December 2012. A high-consequence area is generally an area within a certain distance of a pipeline that has 20 or more buildings intended for human occupancy, or an identified site, such as beaches, playgrounds and recreational facilities. Part of this assessment includes providing provisions to address any problems found, as well as record keeping and reporting.
Threats Assessment
SoCalGas Distribution Integrity Management Program Plan is under development and will focus on information relative to the consideration of the threats to each gas distribution pipeline as well as measures designed to reduce the likelihood and consequences of pipeline failures.
Customer Communications
Many audiences receive our communications, including: customers, excavators and land developers, public officials, colleges, school districts, city and county managers, emergency officials, residents and places of congregation along transmission lines, residents within the distribution service territory, and residents near compressor stations and underground natural gas storage fields. Frequency of communications to each audience ranges from twice a year to every three years.
Our Commitment
You can rest comfortably knowing that the integrity of the pipeline systems that bring natural gas to your homes or businesses is under careful, periodic surveillance. We're doing our part to ensure the integrity of pipelines and will respond quickly to address issues that are identified during regular inspections, surveys, maintenance and patrols.
About Natural Gas Pipelines
Our pipelines transport natural gas received from interstate pipelines and natural gas from California producers to its customers through a complex network of pipelines. Large transmission lines, some as large as 36 inches in diameter and ranging in pressure generally from 200 to 1,000 psig (pounds per square inch above atmospheric pressure), transport natural gas into the population centers where they connect to distribution lines ranging in size from one inch to 20 inches and generally operating at lower pressures. Service lines of one-half to one inch in diameter branch off of the distribution pipes delivering natural gas to homes at less than one-third psig.
The U.S. Department of Transportation (DOT) Pipeline and Hazardous Materials Safety Administration (PHMSA) defines natural gas pipelines under two categories, "Transmission" and "Distribution." Transmission pipelines are primarily used to receive natural gas from suppliers and move it to distribution load centers or to storage facilities. Distribution lines are used to deliver natural gas to customers. These categories are separated primarily by the stress level at which they operate. The Distribution category is further divided into two subcategories: High Pressure Distribution mains, which have a maximum allowance operating pressure greater than 60 psig; and, Distribution mains and services, which have a maximum allowable operating pressure of 60 psig or less. The SoCalGas system ends at the outlet of the meter. The pipes that connect the meter to customer natural gas appliances and equipment's burner tip are typically referred to as the "house lines" and are not owned or operated by SoCalGas.
Distinctive Natural Gas Odor Disclaimer
Some people may not be able to smell the odor because they have a diminished sense of smell, olfactory fatigue (normal, temporary inability to distinguish an odor after prolonged exposure to it) or because the odor is being masked or hidden by other odors that are present, such as cooking, damp, musty or chemical odors. In addition, certain conditions in pipe and soil can cause odor fade — the loss of odorant so that it is not detectable by smell.